What to do when equipment approaches end of life
In order to ensure safe and optimised performance, you need to upgrade equipment before it reaches end of life (EOL). However, such upgrade operations usually need to be planned well in advance. With an EOL policy from your equipment suppliers, you can select a suitable time for upgrading important equipment.
Why is it important to know when EOL approaches?
When you design or operate mission-critical power equipment, knowing when each individual component approaches EOL is very important for two reasons:
- All equipment deteriorates over time, and in order to avoid breakdowns, you need to replace old components before the risk of failure becomes unacceptably high. This applies just as much to electronic equipment as it does to mechanical devices such as pumps or compressors: microchips fail, contacts seize, and sensors become inaccurate. Even with multi-master setups, you need to ensure that all controllers function as they should. If you do not, you could lose redundancy and risk blackouts if all controllers fail.
- Today’s fast-paced technological development means that you and your customers or users could gain other benefits by upgrading components, for example improved fuel economy, better alarm handling, and easier controller programming. Faster processors, improved chip designs, and better software could give you better and faster solutions that are a better fit for today’s requirements.
Base your planning on supplier EOL policies
In short, to ensure safe and optimised performance, you need to upgrade equipment before it reaches EOL. However, such upgrade operations usually need to be planned well in advance. Oil rigs, wind farms, and data centres (to name just a couple of examples) cannot and will not interrupt important operations at moment’s notice to let you replace a controller, for example. This is true even if you own the equipment that needs to be upgraded; it is even more true if you are an OEM with no direct control over your customers’ installations and schedules.
To support your planning, it can be an advantage to use well-defined EOL policies from your equipment suppliers. Such policies will let you know well in advance when a given component becomes obsolete, and when you can no longer get spare parts. With this information, you can work with your customers or users to select a suitable time for upgrading mission-critical equipment such as controllers.
Example: DEIF policy for standard genset controllers
DEIF has defined an EOL policy for standard synchronising genset controller products. It defines the life cycle of a controller product by dividing the life cycle into phases and describing what support you can expect in each phase. A couple of highlights:
- We will endeavour to keep our customers informed of important dates such as the last time buy (LTB) date (the last date where we accept orders for a given product before it enters the obsolete phase).
- We aim at maintaining a reasonable stock of critical wear parts to cover demand for such parts for a period of minimum 60 months following the LTB date for marine approved products, and 36 months following the LTB date for other products.
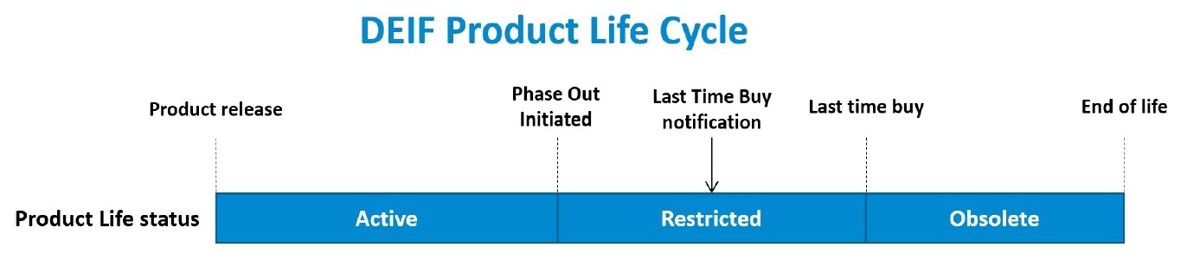
Caption: The life cycle phases of a DEIF genset controller. Our EOL policy defines what happens in each phase, and what kind of support you can expect.
Check the policies that apply to you
EOL policies will vary from manufacturer to manufacturer, and even from product type to product type. In order to ensure a smooth upgrade process for yourself and your customers or users, be sure to familiarise yourself with the policies that apply to you.
On a final note, remember that aftermarket support and clear EOL terms are important aspects of any major equipment investment. In other words: When shopping for new equipment, buy from someone who is ready to provide support for the product throughout its life cycle.
-
Contact us to discuss your options
- 90 years of energy pioneering
- Manufactured at the highest standards
- Superior quality
- Unmatched service and support
- Made in Denmark